지난 7월 4일 SAS코리아는 광화문 포시즌스호텔에서 국내 제조 산업 관계자를 대상으로 ‘SAS 제조 이노베이션 포럼 2019(SAS Manufacturing Innovation Forum 2019)’을 성공적으로 개최했습니다.
SAS는 이번 포럼에서 미국, 독일, 일본 및 국내 제조사들의 고객 사례를 통해 ▲글로벌 B2B 업계의 예측 자산 유지보수 ▲제품 품질 및 투자 수익(ROI) 개선 ▲수요 예측을 통한 생산/판매 플래닝 ▲실시간 품질 예측을 통한 공정 제어 최적화 사례 등을 공유했습니다. 지금부터 포럼 현장 하이라이트를 소개합니다!
첫 번째 세션은 게르하르트 알트만(Gerhard Altmann) SAS 글로벌 제조 산업 프랙티스 부문 수석 디렉터의 발표로 시작되었습니다. 알트만 디렉터는 현대 제조 산업에서 데이터 분석이 지닌 중요성을 바탕으로 자산 성과 분석(Asset Performance Analytics)의 트렌드 및 해외 사례를 소개했습니다.
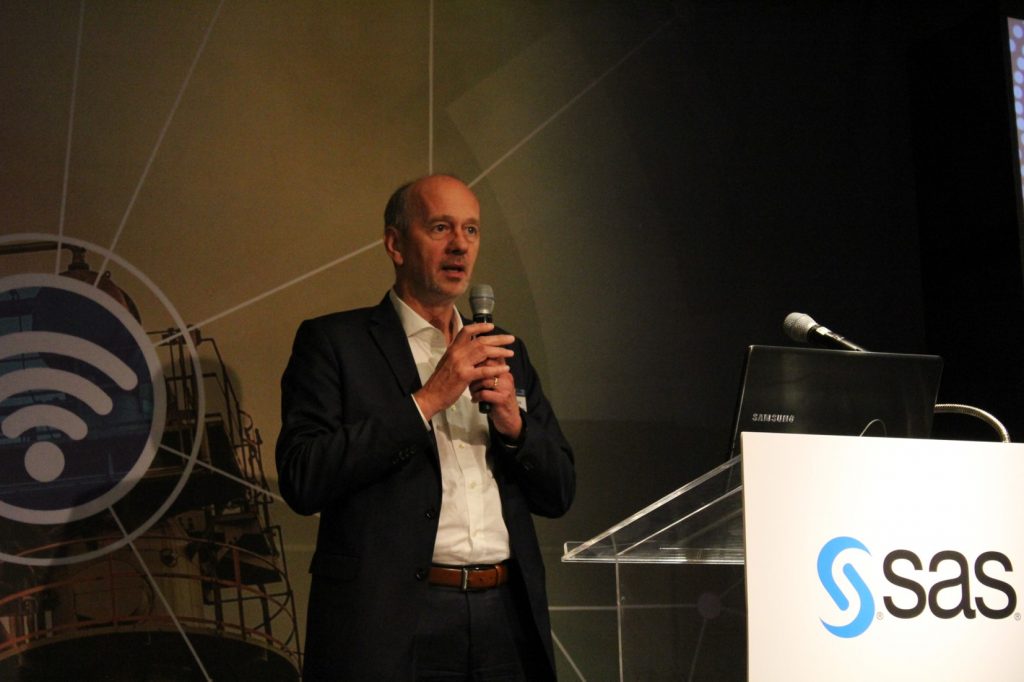
방대한 데이터의 효율적인 관리와 빠른 의사 결정이 기업의 비즈니스를 결정하는 오늘날, 제조 업계 역시 4차 산업혁명을 필두로 디지털 트랜스포메이션(Digital Transformation)을 피할 수 없게 되었습니다. 알트만 수석은 “제조업이 살아남기 위해서는 AI 분석 플랫폼을 구축하여 유지보수 비용과 다운타임(downtime; 고장 등으로 인한 기계의 운행 중단 시간) 리스크를 절감하고 생산성을 향상해야 한다”고 강조했습니다.
실제로 예상치 못한 다운타임은 적시 배송이 필수 성공 요건인 물류 비즈니스에게 매우 치명적이지요. 전 세계 전문 물류 운영을 위한 운송 솔루션을 제공하는 볼보트럭과 자회사 맥트럭(Volvo Trucks and Mack Trucks)은 SAS AI 솔루션으로 사물인터넷(IoT) 데이터 스트리밍을 분석한 후 예측 유지보수 인사이트를 제공해 원활한 화물차 수송 업무를 실현했습니다.
2012년 4천대의 볼보트럭 차량을 대상으로 시작된 원격 진단(Remote Diagnotics)은 오늘날 17만 5천대 이상의 차량을 대상으로 365일 24시간 상시 서비스로 가동됩니다. 볼보트럭과 맥트럭은 SAS의 고급 분석 플랫폼을 통해 데이터를 빠르게 처리, 가동 시간을 향상하는 원격 진단 서비스를 개선해 진단 시간을 평균 70%, 수리 시간을 25% 단축시켰습니다. 이를 통해 커넥티드 차량을 보다 정확하고 효율적으로 운영함으로써 차량 운행 시간을 최대화하는 동시에 서비스 중단으로 인한 손실 비용은 최소화할 수 있었습니다.
두 번째 세션에서는 히토시 츠지(Hitoshi Tsuji) SAS 일본 프리 세일즈 서포트 이사가 브릿지스톤(Bridgestone), 미쓰비씨중공업 항공 엔진(Mitsubishi Heavy Industries Aero Engines), 코니카 미놀타 재팬(Konica Minolta Japan) 3사의 품질 관리 사례를 중심으로 성공적인 디지털 트랜스포메이션을 위해 제조 기업이 명심해야 할 2가지 키워드를 강조했습니다.
- 정확한 목표 설정 및 조직별 전략 수립을 통한 프레임워크(Framework) 설립
- 단계별(Step-by-step) 분석 고도화 작업
츠지 이사는 3사의 분석 플랫폼 구축을 통한 제조 혁신 과정을 입체적으로 비교 분석하며 청중들의 이목을 집중시켰는데요. 한 예로 일본의 사진기 및 복사기 판매사 코니카 미놀타 재팬(Konica Minolta Japan)은 고객 비즈니스 효율을 높이고 고객만족도 향상을 위해 SAS 플랫폼을 도입했습니다. 코니카 미놀타 재팬은 SAS 플랫폼과 AI 솔루션을 활용해 판매, 재고, 고장, 고객 이탈 예측과 유지관리 인원의 행동에 대한 최적화 관리 등의 분석 라이프 사이클 전반을 관리할 수 있게 됐으며 방대한 양의 데이터를 빠르고 정확하게 처리해 계획-실행-검토-개선에 이르는 PDCA(Plan-Do-Check-Act) 업무 속도를 개선했습니다.
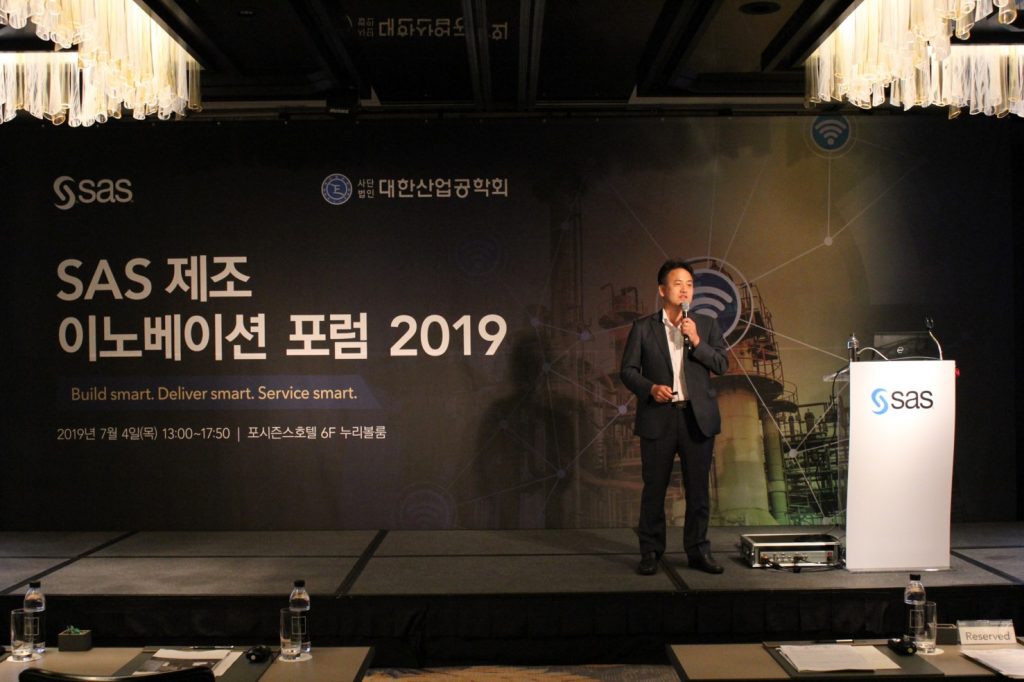
이어진 세션에서는 SAS코리아 고급분석팀 권일형 이사가 국내외 제조사들의 수요 예측(Demand forecasting)을 통한 생산/판매 플래닝 과정을 SAS 비주얼 포캐스팅(SAS® Visual Forecasting) 솔루션을 활용하여 소개했습니다. 권일형 이사는 품목 및 지역별 매출 예측 데모 시연을 직접 선보였는데요. 덕분에 다양한 알고리즘을 동시에 비교 가능하고 예측 결과에 대한 강력한 시각화 분석 기능을 제공하는 SAS 비주얼 포캐스팅의 장점들이 포럼 참석자들에게 생생하게 전달되었습니다.

SAS의 데이터 시각화 솔루션은 ‘코딩 없는 프로세스’를 지향하기 때문에 간단한 클릭과 드래그 앤 드롭(drag & drop) 작업만으로 신뢰할 수 있는 대규모 예측 모델을 빠르게 자동 생성하고, 이를 통해 미래를 대비할 수 있습니다. 이를 통해 분석에 필요한 리소스 범위가 줄어들 뿐 아니라 모든 시계열에 대해 일일이 예측 모델을 구축하고 모니터링할 필요가 없기 때문에, 분석가들은 전략적이고 가치가 높은 예측이나 자동화에 적합하지 않은 문제들에 집중할 수 있습니다.
마지막 세션은 SAS 아시아태평양 지역 제조 프랙티스 담당 최병욱 이사의 ‘인공지능·머신러닝(ML) 기반 SAS 플랫폼을 통한 제조 혁신’을 주제로 진행되었습니다. 최병욱 이사는 데이터-탐색-배치(Data-Discovery-Deployment)에 이르는 SAS 분석 라이프사이클 모델을 기반으로 SAS 플랫폼을 적용할 수 있는 총 8가지 기술 영역과 그에 적합한 SAS 솔루션들을 다양한 글로벌 제조 기업 사례와 함께 공유했습니다.

최병욱 이사는 “디지털 트랜스포메이션 시대의 제조 기업들은 제조 프로세스와 성능을 최적화할수 있는 솔루션을 구축해야 한다”며, “SAS의 AI·ML 기반 분석 플랫폼은 예측을 통해 품질과 공정 상의 문제를 사전에 인지하고, 데이터 통합 및 자동화 과정까지 분석 라이프사이클 전체를 실시간(real-time)으로 지원한다. SAS는 최적화 모델의 실시간 업데이트를 통해 기업 고객이 제조 혁신을 실현할 수 있도록 적극 지원하겠다”고 말했습니다.
이상으로 SAS 제조 이노베이션 포럼의 세션 하이라이트 순간들을 모두 소개해 드렸는데요! SAS는 제조 기업이 품질 및 안정성 문제를 감지하고 해결 및 예측할 수 있도록 SAS 플랫폼을 비롯한 다양한 제조 산업을 위한 솔루션을 제공해오고 있습니다. 앞으로도 첨단 AI, 머신러닝, 스트리밍 분석 등 최신 기술과 솔루션을 통해 혁신을 이어나갈 SAS의 여정에 많은 관심 부탁 드리겠습니다. 🙂
1 Comment
잘 봤습니다.