Manufacturing remains a transformative process at its core, converting raw materials into valuable products.
While the fundamental essence of manufacturing has endured for centuries, the methods and technologies employed have undergone significant evolution, driven by innovation and the ever-shifting demands of consumers.
As we enter 2024, the manufacturing industry is abuzz with predictions and trends, with experts, analysts, and consultants eager to identify the next big thing. Discussions have revolved around machine learning, digital twins, generative AI, factory automation, autonomous production, and the potential replacement of humans by robots. Amidst this flurry of excitement, it's crucial to approach these trends with a discerning eye, ensuring a balanced focus on timeless principles and timely trends.
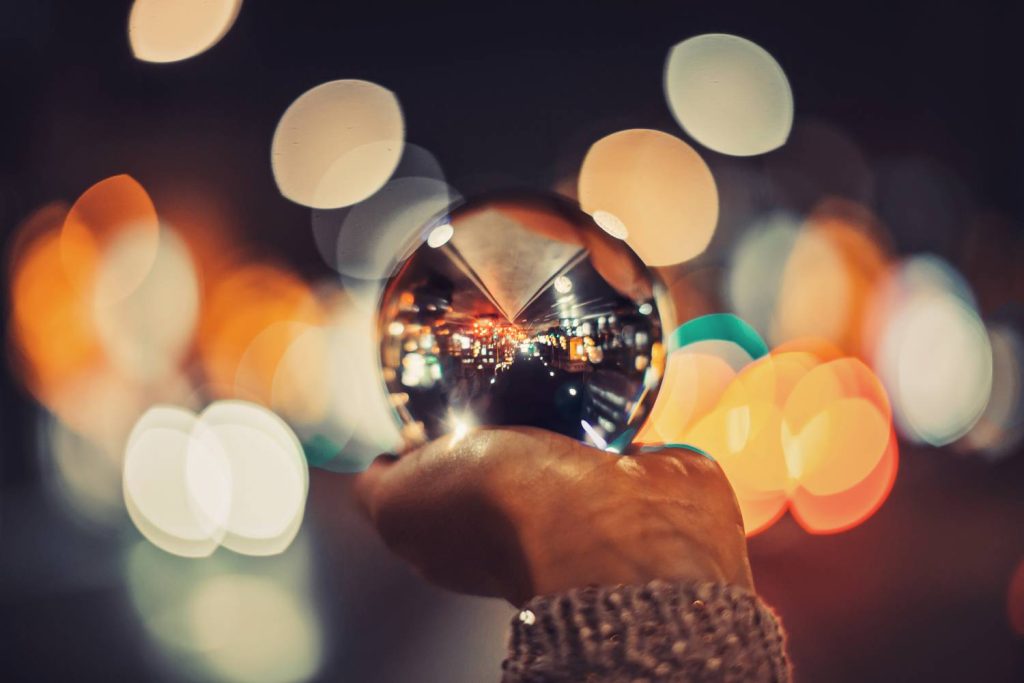
Timelessness refers to the enduring principles that underpin successful manufacturing, such as quality, efficiency, and customer satisfaction. These principles have guided manufacturers for generations and will continue to be relevant in the future. On the other hand, timeliness acknowledges that manufacturing is constantly changing and shaped by technology, markets, and global forces.
As we delve into 2024, several key trends are poised to shape the future of manufacturing, impacting productivity, sustainability, and workforce dynamics. Let's examine three of these trends in detail:
Trend 1: The rise of smart factories
A Deloitte report forecasts a global smart factory market reaching $576 billion by 2028, driven by the increasing adoption of Industrial Internet of Things (IIoT)-enabled devices and the growing demand for real-time data analytics. Smart factories revolutionize manufacturing operations by leveraging advanced technologies such as IIoT, AI and machine learning to create a highly connected and data-driven environment. These technologies help manufacturers optimize production processes, predict and prevent equipment failures, and personalize products to meet individual customer needs.
While larger organizations may have the resources to pursue these new technologies and approaches, smaller organizations can still embark on their smart factory journey by starting with what they have and iterating. If advanced AI platforms are not readily available, a set of if-then rules, standard operating procedures and regressions can be effective substitutes.
Trend 2: Growth of predictive maintenance and digital twins
A 2022 report by the Society of Manufacturing Engineers estimates that predictive maintenance can reduce unexpected failures by up to 90%. Predictive maintenance, powered by AI and ML, is transforming how manufacturers maintain their equipment. By analyzing real-time data from sensors and machines, predictive maintenance systems can identify potential problems before they occur, preventing costly downtime and unplanned repairs.
Digital twins, virtual replicas of physical assets, also play a crucial role in predictive maintenance. By simulating real-world equipment behavior, digital twins help manufacturers predict and optimize performance, extending asset lifespans and reducing maintenance costs.
While predictive maintenance is a timely trend, it aligns with the timeless principle of asset life maintenance. Manufacturers should strive to have well-trained maintenance staff and schedule regular maintenance outages to ensure optimal equipment performance.
Trend 3: Importance of reshoring and supply chain resilience
The COVID-19 pandemic and ongoing geopolitical tensions have highlighted the vulnerabilities of global supply chains. In response, manufacturers are increasingly looking to reshore production, bringing operations closer to their customer base to reduce risks and improve supply chain resilience. A 2023 report by the Reshoring Institute indicates that reshoring is at an all-time high in the United States, with companies seeking to reduce reliance on overseas suppliers and gain greater control over their supply chains.
Supply chain leaders have always prioritized resilience, employing redundancy, diversification, and forecasting strategies to maximize customer satisfaction and business performance. As we move into the future, these core strategies will only improve by adapting modern technologies like analytics and AI.
Looking ahead to 2024
These three trends – smart factories, predictive maintenance and reshoring – represent significant shifts in manufacturing, driving innovation and enhancing competitiveness. Manufacturers that embrace these trends will be well-positioned to navigate the challenges and opportunities of the future.
However, it's important to remember that while timely trends are valuable, timeless principles remain the foundation of successful manufacturing. By striking a balance between the two, manufacturers can ensure their operations remain relevant, efficient and sustainable for years.