From the discovery of LED lighting to the rise of robotics and 3D printing, technology continues to transform the manufacturing industry. Yesterday, it was the assembly line. Today, it’s digital twins.
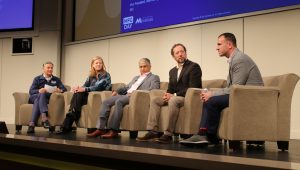
In particular, technology developments in the data and analytics space were discussed at a recent MFG Day held at SAS World Headquarters in Cary, NC. Panelists from Deere & Company, Mack Trucks and Johnson Controls International each explained how the use of analytics is continuing to transform the industry.
The proliferation of IoT data on the factory floor – and the collection and use of that data – has blurred the lines between blue-collar and white-collar workers, explained Govi Kannan, Senior Vice President of Global Products & Technology at Mack Trucks. “Now we have ‘new collar workers’ or ‘collarless workers’ in all areas. Someone standing at the assembly line is now sitting on a ton of data at the point of build.”
Virtual manufacturing reimagines innovation
According to Kannan, the advancements in computational power and communication power are ushering in exciting developments in the world of analytics, like digital twins: “Today, before we put a truck on the assembly line, we can have a digital twin of that truck that we can work on in our laboratory.” This digital representation of the physical truck gives Mack Trucks an economically viable way to detect early interference design issues and to solve any potential quality problems before they even build parts.
“Virtual manufacturing means we can have experts sitting in different parts of the country – or even the world – working on these projects,” said Kannan. “Technology is changing the way we are building products. Today, data, communication and computation are all coming together at the point of build.”
At Deere & Company, Tami Hedgren, Vice President and Manufacturing Lead of Large Truck and Combines, said virtual builds are being used to examine ergonomic features, process flows, material flows and more. “When you think about analytics, it’s used across the board from supply chain all the way through to manufacturing and aftermarket customer support.” Analytics even makes autonomous tractors possible, explained Hedgren.
“No matter where you are in manufacturing, analytics plays a role. We’re working on uptime on machining, automated material flows, steel prices, labor costs and more. It’s in all aspects and changing the way we work to take the industry to the next level.”
Analytics improves speed and agility in solving problems
People and their ability to problem solve are still the foundation of manufacturing, says Brandon Wagner, Executive Director of Operations at Johnson Controls International. But he adds, analytics can only improve and speed up those skills.
“What I’ve seen as the biggest change is the speed in which we can drive change,” said Wagner. “What used to take us quarters or years to do, now we’re doing in days and weeks and months. That speed is very, very impressive and a lot of fun actually.” Employees who are resistant to change can pose a problem, but Wagner said that’s where it’s important to have the right culture and the right mindset. All of these things will be important to embrace the industrial internet of things (IIoT), robotics and continuous improvement.
Kannan summed up the importance of applying analytics to manufacturing data by saying, “Technically, yes, we are in the business of trucks, but more than that we are in the business of data. Data is going to work its way into every aspect of what we are doing.”
Being able to transition from data to insight to action will be crucial for success of all manufacturers moving forward, explained Jason Mann, Vice President of the Internet of Things at SAS. “The big opportunity for manufacturers is to generate intelligence from that massive amount of data. I focus on the IoT area, and the idea is that now decisions are expanded from the edge device, right where the data is created all the way into the cloud or on premise. Now you’re integrated with insight that you just never had before, and being able to act on that has been the real difference for many manufacturers.”