Industry 4.0 has become a watchword for manufacturers, but I’m not sure the implications are clear to many. Hyperconnected customers are the fundamental premise of Industry 4.0 and they expect more than good quality. They expect their manufacturers to also behave like retailers and service providers.
Real-time and predictive engagement is becoming much more of a ‘must-have’, rather than a ‘nice to do’ as part of any manufacturer’s customer experience. Customers expect a more personalised service. But this makes a huge difference to the analytics platform and capabilities for manufacturers and their services journey.
Understanding the requirements
For a start, manufacturers need to be able to integrate data from as many sources as possible. This is not trivial, not least because of the sheer volume of data involved. The Internet of Things (IoT) is expected to generate so much data that it can be likened to a tsunami. There are also a number of different types of data, from input to usage, as well as streaming data, and this complexity will only grow. Versioning and APIs, to mention just two issues, can create difficulties within enterprise IT structures, particularly in the manufacturing sector. Speed of use is also important: customers expect businesses to have answers quickly.
Manufacturers also need to be able to understand the signals from devices and particularly to detect patterns as events occur. The responses required could be extremely simple, such as an alert, or much more complex and/or automated. This means being able to run complex models, and rapidly.
Addressing the fundamentals
There are, of course, issues to address. First and foremost, manufacturers need what I see at an “analytics platform”. Without that, nothing else follows. One question is whether manufacturers are actually seeing this requirement in terms of a platform, rather than a loose connection of existing tools and capabilities. A platform is likely to be important for long-term capabilities, even if tools are enough in the short-term.
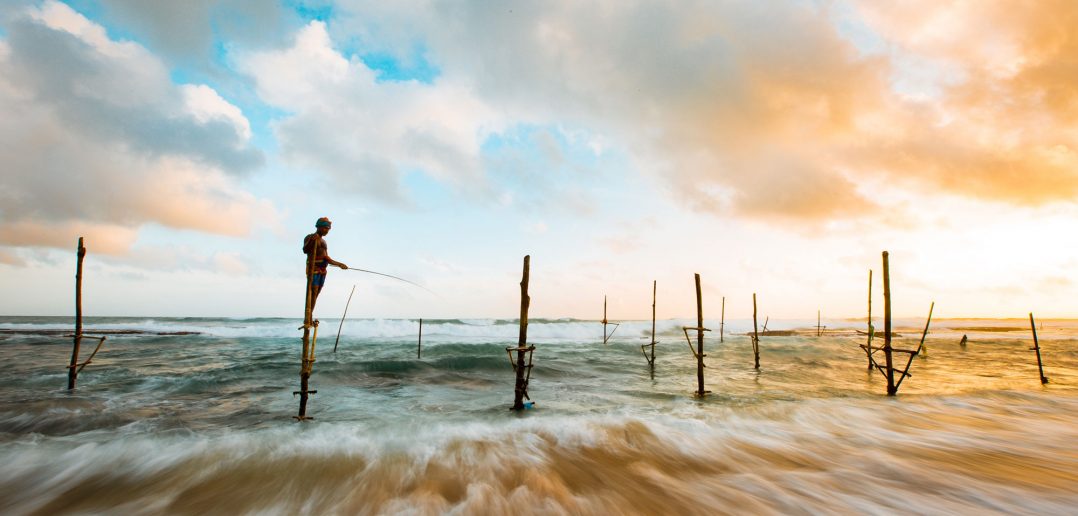
Using a platform is also an indicator that manufacturers recognise that they are on an analytics journey. This change in mindset is likely to be important in taking advantage of the opportunities available. Opening up the platform to everyone within the company, and not just trained analysts or data scientists — democratising analytics — will increase the value obtained from investment in analytics. After all, there are very few data scientists available, and far more other employees. It is hard to embed a data-driven mindset without providing ready access to data and analytics.
There are, however, fundamentals of use to resolve as well. For example, not all consumers want a personalised response, and some find this move downright ‘creepy’. Manufacturers need to understand this, and respect this preference just as they do with others. Resolving issues of data privacy and protection are fundamental to succeeding in this market. Failure to do so could result in a loss of the market altogether, not least because governments could step in with regulations, such as GDPR in Europe.
Manufacturers also need to consider storage and use of data. Analysing streaming data close to source means that the data do not need to be stored in the longer term, which saves on capacity and bandwith. However, there is a real question about whether real-time is always the right time for analysis, or whether cleaning data for later use can give even more insights into different areas. It may be that storage is essential, at least for a while, to obtain full value later on.
It is hard to embed a data-driven mindset without providing ready access to data and #analytics . #AnalyticsPlatform Click To TweetTaking advantage of the potential
Once a suitable analytics platform is in place, it can support much more than simple improvement of customer experience, important though that is. For example, real-time engagement and analysis has huge security breach prevention potential. This is a major change of pace from the previous approach that either put barriers in place to stop likely fraudulent access, or managed the results after the event. Indeed, perhaps we should not separate cyber security from customer experience, because security is high on most consumers’ list of essentials. Knowing that the company is taking action to prevent non authorized acces can be a major selling point.
Streaming data can also allow manufacturers to follow devices throughout their lifecycle. Data from this process can be fed back to improve manufacturing, but it is also an important part of ongoing quality assurance, and even predictive maintenance. This, too, helps better understanding customer voice.
There is no question that real-time and predictive engagement are already changing manufacturing companies and customer expectations around the world. The real question is how best to take advantage of the opportunities, and generate maximum value from investment in suitable & democratized analytics platforms.
2 Comments
Manufacturers also need to be able to understand the signals from devices and particularly to detect patterns as events occur. The responses required could be extremely simple, such as an alert, or much more complex and/or automated. This means being able to run complex models, and rapidly.
Indeed Muhammad, and that's why this analytics platform is often used in conjunction with streaming or edge analytics (for instance SAS Event Stream Processing) which allows to run quick and reliable models but also timely track their performance.