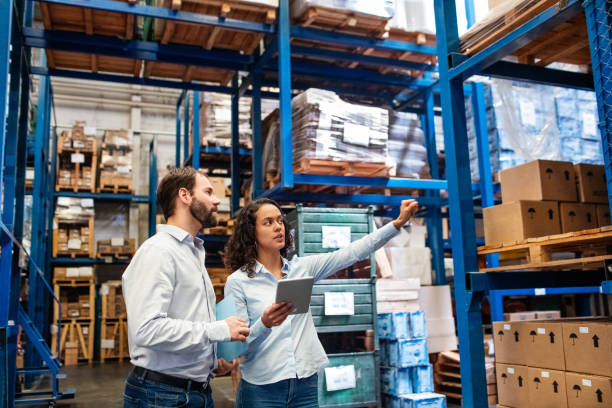
å»è ã®èšºæã«äŸããŠåŠã¶ AIãçšããã»ã³ãµããŒã¿åæã·ã¹ãã ã«é¢ãããããã誀解ã«ã€ããŠ è£œé æ¥ã§çãã«å°å ¥ãããŠããã»ã³ãµããã®ã»ã³ãµããŒã¿ãåæããŠããžãã¹ã€ã³ãã¯ãã®ããçµæãåºãã«ã¯ãã©ã®ããã«ãããè¯ãã®ã§ããããïŒ ããŒã¿åæãæåãããããã«ã¯ãæ§ã ãªèŠçŽ ãèããããŸãããããã§ã¯ã»ã³ãµããŒã¿ã®è³ªã«æ³šç®ããããšæããŸãããããé«åºŠãªããŒã¿åæææ³ãçšããŠããåæå¯Ÿè±¡ã®ã»ã³ãµããŒã¿ãæ£ããååŸã§ããŠããªãå Žåã¯ãçµæãåºãªãããšã¯å®¹æã«æ³åã§ããŸãããããŸãè°è«ãããããšã¯ãããŸããããããã¯ãã»ã³ãµèšæž¬ãšããŒã¿åæã®äž¡æ¹ãèŠéã«å ¥ããå¹ åºãããŠããŠãå¿ èŠãšãªããInformation Technology (IT) ãš Operational Technology (OT)ãšã®èåãšãã課é¡ã«è¡ãçãããã§ãã æ¬ããã°ã§ã¯ããã®ããã¢ãã¯ãªè©±é¡ããå»è ã®èšºæã«äŸããªããããããããã解説ããŠãããŸãã èšäºã®æ¯ãè¿ãïŒãèªèŠçç¶ãç¡ãã»ã³ãµããŒã¿ã®å質åé¡ ãããŸã§ãèªèŠçç¶ãç¡ãã»ã³ãµããŒã¿ã®å質åé¡ããããŒããšãããã»ã³ãµããŒã¿ã®å質ãåäžããã7ã€ã®ãã€ã³ããã«ã€ããŠïŒåç·šïŒãšïŒäžç·šïŒã®2åã«åããŠã話ãããŸãããçç£ã©ã€ã³ã®DXã®ããã«ãã»ã³ãµããŒã¿ãçšããŠããŒã¿åæãããŠããã®ã ããæããããªçµæãåŸãããŠããªãã±ãŒã¹ãåžå Žã§çºçããŠããããšããäŒããããã®åå ã®äžã€ãšããŠãåæå¯Ÿè±¡ãšãªãã»ã³ãµããŒã¿èªäœã®å質åé¡ãããããšããäŒãããŸããããã®åé¡ã¯é¢ä¿è ãæ°ä»ãã«ãããå¯ŸåŠæ¹æ³ãå°éç¥èãšçµéšãå¿ èŠãšãªããŸãããä»åã®åŸç·šã§ã¯äžèšã®â¥ïœâŠã«ã€ããŠåŸ¡èª¬æããŸãã å³ïŒ. ã»ã³ãµããŒã¿ã®å質ãåäžãããïŒã€ã®ãã€ã³ã â¥ããŒã¿ã¬ã€ã¯ã«èç©ãã¹ãããŒã¿ã®éžæïŒç¹åŸŽéæœåºïŒ ãããŸã§ã®èšäºã§ã課é¡è§£æ±ºã«ãããããé«å質ãªã»ã³ãµããŒã¿ãåéããããšãéèŠã ãšè¿°ã¹ãŠããŸããããä»ã«ãéèŠãªãã€ã³ãããããŸããããŒã¿ã¬ã€ã¯ã«èç©ãã¹ãããŒã¿ãã©ã®ããã«éžæããã®ãããæšä»ã課é¡ãšãªã£ãŠããŸãã ãçç±ãšããŠã¯ãAIã¢ãã«éçºãšæŽæ°ã®ããã«ãããçšåºŠã®çããŒã¿ä¿åãå¿ èŠãšãªãããã§ããããã®åé¡ã¯ãPoC段éã§ã¯å€§ããªåé¡ã«ãªããŸãããPoCãšç§°ããŠå€§éã«ããŒã¿ãåã£ãŠå°éã®æ åœè ãè§£æããããã§ããåé¡ã¯PoCåŸã®çŸå Žã§ã®éçšã§ãã å³ïŒ. é¢é£ããŒã¿/ã»ã³ãµ/ç¹åŸŽéã®æŠç¥çéžæ ãããã¯ãªãã§ããããïŒãåçš®ã»ã³ãµãäœãåºãããŒã¿éã¯éåžžã«å€§ãããã»ã³ãµã«ãã£ãŠã¯æ¯å1 GB 以äžã®ããŒã¿ãçæããŠããŸããéä¿¡ãããã¯ãŒã¯ã®è² è·ã®åé¡ããã¯ã©ãŠãäžã§ã®ããŒã¿ä¿åã®ã³ã¹ããšãã£ãçŸå®çãªåé¡ãèŠããŠããããã§ãããäŸãã°ãå³ïŒã®å³åŽã®è¡šã«ç€ºãããã«ããµãŒã¢ã°ã©ãã£ã¯åç»åã®ããã1åéã§1GB以äžã®ããŒã¿ãçæããŸãããã®å ŽåãåŸé課é/ãããã¯ãŒã¯ãã©ãã£ãã¯æžãžã®å¯Ÿå¿ãå¿ èŠãšãªããŸããæž©åºŠã»ã³ãµçã®ããŒã¿éã¯ãæ°åã§ããã°å°å®¹éã§ãããæ°çŸåãã»ã³ãµã䜿çšããã±ãŒã¹ã§ããšãïŒåéã«æ°MBã«ããªããŸãããã®ãããªããŒã¿ãã¯ã©ãŠããžè»¢éãç¶ããå¿ èŠãããã®ã§ããããïŒ ãŸããé«é¡ãªã»ã³ãµãæžããããã«ãã§ããã ãã»ã³ãµã®æ°ãçµããããšããèŠæãåºãŠããŸãããããããããããŒã¿éžæïŒç¹åŸŽéæœåºïŒãã©ããããã®ããšãã課é¡ã®æ¬è³ªã§ãããããŒã¿åæäžãç¹åŸŽéã®éžå®ãéèŠã ãšããçç±ãšã¯ç°ãªããŸããã§ã¯äžäœãã©ããªããŒã¿ãæ¬åœã«å¿ èŠãªã®ãããŸãããŒã¿éãæžããæã«ã©ã®ãããªåœ¢ã§ãšããžã³ã³ãã¥ãŒãã£ã³ã°ã掻çšãã¹ããªã®ã§ããããïŒ ãã®æè¡çãªèŠè§£ã¯ãä»åŸãããã°ã«ãŠç޹ä»ãããŠé ããããšæã£ãŠãããŸãããITãšOTã®äž¡æ¹ã®èŠç¹ããæ€èšããå¿ èŠããããŸãããããŒã¯ãŒããšããŠã¯ããåå£«ã®æèŠäº€æã§ãã âŠããåå£«ã®æèŠäº€æãéµãšãªã ãããŸã§ãã»ã³ãµããŒã¿ã®å質ãããŒã¿åæã«äžãã圱é¿ã«ã€ããŠãããŒã¿åæäŒæ¥ã®èŠç¹ã§è¿°ã¹ãŠããŸããããã©ã®æ³šæç¹ãå°éç¥èãšçµéšãèŠãããã®ã°ããã§ããã€ãŸããæåã®éµã¯ãããåå£«ã®æèŠäº€æã ãšèšããŸãïŒå³ïŒïŒããããã¯ãæ¥çãè¶ ããã³ã©ãã¬ãŒã·ã§ã³ã®å¿ èŠæ§ãããITãšOTãšã®èåãéµã«ãªãããšè¡šçŸããŠãè¯ããããããŸããã ç¹ã«çŸå Žã®çç·Žè ãšã®åæ¥ã¯å¿ é ãšãªããŸããçŸå Žã®çç·Žè ãã䌺ãããäºãšããŠã¯ã枬å®å¯Ÿè±¡ç©ã®è©³çްã補é ããã»ã¹ãäœæ¥å·¥çšãç°åžžç¶æ ã®è©³çްããŸããã©ãããã¡ã«ããºã ã§ç°åžžãèµ·ããã®ãæ å ±äº€æãããŠé ãããšãéèŠã§ãããããŠããããã©ãã ãå°ãããšãªã®ãããããžã§ã¯ãããŒã å ã§æèŠäº€æãããŠé ãããšãéèŠã ãšèšããŸãããããŠãã»ã³ãµããŒã¿åéããããŒã¿åæãŸã§ãåºãèŠæž¡ããäžã§ãAIãçšããã»ã³ãµããŒã¿åæã·ã¹ãã ãæ§ç¯ããŠããããšãæåãžã®è¿éã ãšçè ã¯èããŠããŸããé£ããæããããæ¹ããããããšæããŸããããã®ããåå£«ã®æèŠäº€æã«é¢ããŠã¯ãæ¥æ¬äººãšã³ãžãã¢ãåŸæãšããé«åºŠãªæŠãåããæåãæŽ»ããããšä¿¡ããŠãããŸãã å³ïŒ. ããåå£«ã®æèŠäº€æãå€§äº ã以äžãã»ã³ãµããŒã¿ã®å質ãåäžãããïŒã€ã®ãã€ã³ãããïŒåã«åããŠç޹ä»èŽããŸãããæ°ã«ãªãç¹ãããããŸããããåŒç€ŸãŸã§ãåãåããäžããïŒ ååã®ããã°