Robert Handfield, PhD, is a distinguished professor of Supply Chain Management at North Carolina State University and Director of the Supply Chain Resource Cooperative. In an episode of the Health Pulse Podcast, Handfield gave his views regarding the challenges health care and life science companies have encountered over the past two years due to several unforeseen disruptions.
COVID-19, the China trade wars, climate change and the Russia-Ukraine war have disrupted global supply chains. We will continue encountering periodic disruptions beyond 2022 into 2023 and possibly beyond.
As a result, companies will need to learn how to become more agile by developing more interesting solutions through double sourcing, redundancies, nearshoring and using new technologies like supply chain digital twins.
Rethinking just-in-time (JIT) delivery practices
Companies are rethinking their overall supply chain systems in health care due to the supply shortages caused by COVID-19. Everyone agrees that we need to have healthier national stockpiles, alignment, agility, and training to understand better how to handle future disruptions, as another is very likely on the horizon.
All of the supplies the US needed to deal with the pandemic, including ventilators, were sourced in one region, Asia. China and other Asian countries shut down during the pandemic and halted all their exports to the US. As a result, the US was dependent on a global supply chain that we thought was built based on a just-in-time (JIT) supply chain system.
When manufacturing facilities and suppliers worldwide don't have enough inventory, that's not just-in-time. That's the opposite. It's only JIT if you have manufacturing facilities strategically placed worldwide and supported by local suppliers. The true definition of JIT requires that you have local suppliers that are close to your manufacturing facilities that deliver daily, as well as multiple times a day. The manufacturing facilities are also in direct communication with the local suppliers. A good example happened in 2020 when Pfizer partnered with more than 300 suppliers and added 44 qualified and capable small businesses, significantly increasing diversity within their supply chain and making it more resilient.
After two years of disruptions, what have we learned?
Healthcare providers have gone in the opposite direction where they are now leasing warehouses and stuffing them with six months of inventory.
Handfield mentioned concerns about 3M's N95 mask shortages during the pandemic, which was related to China's production of most of those masks. What's even more interesting, during the pandemic, several US manufacturers started to make masks domestically. As the pandemic began to wind down, many manufacturers went bankrupt as their prices were higher than masks made in China. As China started to reenter the US market, the US health care providers returned to purchasing lower-cost Chinese-produced masks.
Who has been able to adapt and build supply chain resilience?
Although there haven't been numerous updates in the health care or life sciences industries, there are many changes in motion to improve their overall supply chain resilience. One organization, the Cleveland Clinic, has created innovative models that help hospitals forecast patient volume, bed capacity, ventilator availability and more with SAS technology using predictive analytics and scenario planning. That's a real game-changer to use analytical technologies to run those real-time scenarios to uncover bottlenecks and choke points in the supply chain. They are using predictive analytics to understand better what could happen and how to plan better to prepare for the next disruption.
As we emerge from this latest wave of the perfect supply chain storm, many organizations ask, "what can we do differently?" Those same organizations are now contemplating how to connect the physical supply chain to the digital supply to run real-time simulations to circumvent future disruptions.
What can companies do immediately to shore up their supply chain?
Companies realize the benefits of advanced analytics and machine learning by connecting their physical supply chain to a digital supply chain replica to create real-time simulations to determine bottlenecks and choke points before they occur using digital twin technology.
Digital twins are replicas ranging from physical objects to complex ecosystems. A digital twin replicates an organization's ever-evolving functions, including physical entities, financial assets, human resources, processes, workflows and constraints. Using digital twin simulation technology, companies can test unlimited scenarios demonstrating the impacts of different decisions on operational efficiency and KPIs across their supply chain network.
SAS and Cosmo Tech innovations build resilient global supply chains. Uniting analytics with digital twin simulation strengthens future performance in uncertain times.
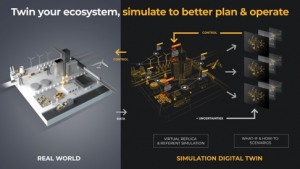
A supply chain digital twin can be used for:
- Understanding supply chain dynamics and behavior.
- Bottleneck and choke point discovery.
- Testing supply chain design changes and development.
- Monitoring risk and testing contingencies.
- Transportation planning
- Inventory optimization, replenishment, and allocation.
- Forecasting and testing operations are planning over the coming days and weeks.
An agile supply chain is a competitive advantage and represents a robust use case for digital twins. Health care and life science companies can use digital twins to apply machine learning across numerous data streams to simulate the real-time movement of goods, material flows, inventory positions and warehouse operations.
Is globalization over?
Are companies going to onshore more of their manufacturing and supply chain capabilities locally by country? Supply chains are not all the same or can be interchanged or moved around the world. There are certain types of products that we must continue to rely on China to produce and manage. We've outsourced so much to China because they are much more efficient in producing specific categories of goods and services. We are seeing something called "nearshoring," or in some cases, double shoring, where companies use a secondary supplier.
One nearshoring supplier for North America is Mexico. Mexico is a truck drive away, has an excellent workforce, and its labor costs are lower than China's. When you consider the cost of transportation (China container costs are roughly $8,000—Shanghai to LA), the savings are much lower, which is significant. Plus, the US has free trade agreements with Mexico and Canada.
Handfield feels companies will start to see a movement toward a Pan-North American supply chain. There's lots of capital, labor and energy in North America, making it a great combination to build a more efficient and effective supply chain. He believes this will result in more "resilient, adaptable supply chains."