A conversation with the Senior Vice President at BASF, who is responsible for the global business unit Oilfield & Mining Solutions, Damien Caby, is more than exciting. He let us look behind the scene at the role of artificial intelligence in the oilfield and mining sector. And he answered the question of how AI will contribute to the industry in the future with a special focus on skill shortages.
Damien, artificial intelligence (AI) is mainly used to optimize processes, where do you see opportunities for the mining industry?
AI is helping to transform the mining industry. In the past decade, the increased adoption of AI has been improving the efficiency and effectiveness of mining operations. Furthermore, it is making mining more environmentally friendly and safe. We are seeing mining processes change significantly as more AI tools become available. More mines are beginning to use computer-driven technology alongside their equipment to help their people operate better while reducing safety hazards. Mining is very costly too, so AI is being used to optimize the mine-to-market value chain. Better AI recommendations or predictions result in better planning affecting a plant’s bottom line.
A perfect example of such a solution is the BASF Intelligent Mine powered by IntelliSense.io. Our product allows mines to gain the information they need by leveraging the power of digitalization. Information can be easily accessed, and simulations can be run to mitigate risk. Imagine being able to run scenarios on the computer before doing it in real life, this is what the BASF Intelligent Mine is, a very powerful tool that enables innovation.
We offer a unique “out of the box” solution that delivers maximum value at implementation as 80% of the work has already been done by mineral processing experts building a suite of products specific to each processing step which are assembled into al solution tailored to each of our customers’ specific flow sheet and industrial layout.
Industrial AI-technology – Does this go hand in hand with data analytics? How is the usage of both technologies differentiated?
It’s not a matter of one or the other, it is important that we understand the benefits and limitations of using AI vs data analytics. Data analytics are extremely useful. It starts with understanding the situation of the mine and unlocking the value of operational data by diving into it. Mines can review historical data and use their judgment and understandings of the past to create and test their assumptions. The downside is that people are limited on time and cost constraints.

AI technology can analyze data, make assumptions, and provide predictions. All of this is possible without the intervention of humans and is done at a speed and proficiency that no human can compete with. This changes everything since the complex analysis can also be done using several variables. For us, data analytics comes always before we recommend using AI. In our experience, it starts with understanding the situation of the mine and unlocking the value of operational data by really diving into it. With that we can evaluate the quality of the data, set the quality needed and what kind of relations we have in a data set. AI is always the next step based on the parameters and studies pre-defined by the data analytics analysis.
How can AI contribute to the mining industry in the future?
We all know that AI has been around for quite some time, but the applicability of AI is constantly advancing. Many companies, including mining companies, are working to understand how to integrate this powerful technology into their daily operations. What AI can do today will be improved over time, allowing mines to continue to make real-time decisions to optimize their plants. Mine operators will be able to better control their whole site at elevated levels. Moreover, AI contributes to sustainability and environmental benefits allowing mines to “Go Green” as much as possible to protect the environment as we mine much-needed resources.
Do you have an example?
Sure, in a mineral processing plant we see, that the thickener circuit recovers water from the process waste (tailings), which improves the environmental performance of the mine site, as water is a precious commodity. The more water that can be recovered, the less water the mine site must import. The industry can use AI-based controls or recommendations to improve the overall performance of a thickener. By applying AI solutions, a mine operator can predict how a thickener will behave into the future, let’s say one hour, and then make changes to the current controls to avoid poor performance. This combination of prediction and then optimization in real-time is the hall marl of AI, performing significantly better than its human counterpart.
In the future AI systems will be able to support the entire mining process chain, giving insight, predictions, and optimization to processes that are currently too complex for human operators to optimize in real-time. The result is a more stable operation, running faster, with fewer interruptions, and producing more output with fewer resources and a lower environmental footprint. Energy, waste, raw materials, chemicals, and manpower can all be optimized to make the operation more sustainable.
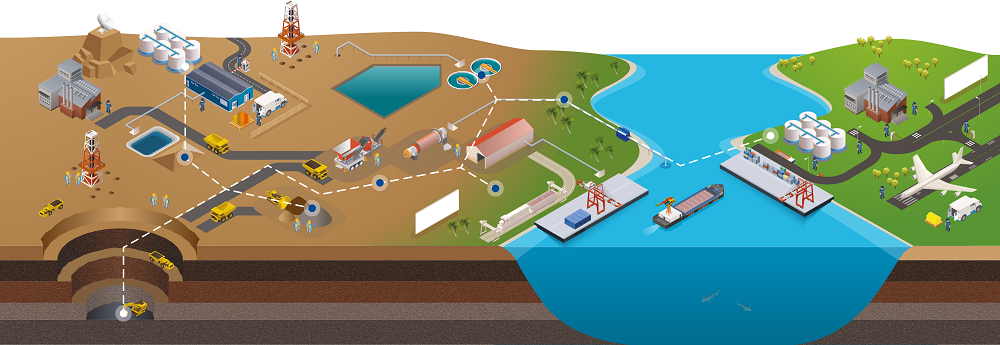
Which processes need the contribution of AI at a mine site, which AI solutions will they never need?
AI solutions can only be applied to applications that have an appropriate data set that allows for the advanced insights, predictions, and optimization possible with AI. Clearly, some parts of the mining process have more data that is usable than others. These mature areas of the process are where AI is beginning to be applied today. These processes have good instrumentation and process control, which support the ability of AI solutions to find interesting and complex relationships and provide useful insights.
The next area of expansion for AI systems is processes that have instrumentation and process control systems that are less reliable. This unreliability can be caused by many factors, like harsh conditions of temperature, pressure, chemistry, or even the lack of instruments. AI can be successfully applied to these challenges. By combining AI with other physics-based models, new insights can be developed. AI systems can then start to make predictions and recommendations based on poor or incomplete data. This is extremely powerful and offers some of the biggest future value to optimize these processes.
... the flotation circuit?
Indeed, this is one area on a mineral processing plant that can significantly impact revenue. It is therefore critical that this process is controlled and operated at its optimum. Typically control on a flotation circuit is reactive as lab assays give operators and engineers feedback on metal recovery, losses and, product grade. Operational parameters are then adjusted in response to these assays, which may be outdated and no longer representative of what is actually happening live on the flotation circuit. As these assays do not relate to the performance of individual cells but to the unit process as a whole, it is difficult to see if a particular cell is performing poorly. By applying AI solutions like the BASF Intelligent Mine Flotation Application, operations are optimized adding much-needed transparency and insight on process performance via virtual sensors. These AI-based assets provide previously unmeasurable data for variables like individual cell recovery, gas hold-up, and air bubble diameter. From inputs such as feed flow rate and other known parameters, the models can be configured to provide visibility on individual cell performance. This means that poor-performing cells can easily be identified, and problems quickly rectified, minimizing losses. This optimizes the circuit’s performance and maximizes revenue by maximizing recovery whilst maintaining grades.
How does the industry interact with universities to prepare students for new technologies?
Now that AI is a growing force in our global economy, we can estimate that most companies will adopt at least one type of AI technology at some point in the future. Given this information, as the mining industry begins to adopt AI more, the new workforce will need to be up to date on what is available and how it works. Universities are aware of this and are working to qualify the next generation of mining employees. The mining industry has always collaborated with universities by sponsoring university programs, lecturing, or subsidizing internships and we can ensure that AI will be a topic of much discussion.
Could you please share some more details about the academic education for the mining industry, how do you rate it?
Academic education in mining is excellent and present in several countries worldwide. However, in some countries like Germany and the UK, the mining presence is declining. The availability of mining courses in universities tended to decrease following the mining trend. Now, with the AI technologies emerging alongside data science in this area, new courses are being created to push this trend. The strong mining history and knowledge of those countries are clearly supported by the courses created in the educational sector.
Do you experience a skill shortage in the field of AI in mining or do you think that new technologies increase attractiveness that there is no risk of skill shortage?
Mines have always been challenging places to work and this will only increase as the industry continues to move deeper into harsher environments. The use of AI will reduce the need to put people into these severe conditions. Therefore, the implementation of new technologies, like AI, is illustrating that the mining industry is committed to sustainability and they are creating a safer mining operation for their people.
The use of AI can and will replace some mining jobs but will also lead to countless new jobs in the field of AI. Working in mining will be more attractive since the old way of mining is changing. We are seeing this restructuring happening in the world of mining today. So, the mining industry is pushing for skilled people that understand AI and want to be part of this exciting transformation.
One of the challenges miners and companies like BASF who support the industry has had in the past is attracting good quality technical staff to our operations. AI professionals, like STEM, are not used to working in remote and challenging environments like mine sites. The advantage of Industry 4.0 has been and will continue to be, the development of remote operations. This approach for mining means we can house our valuable technical people away from the mine, in cities, or other more desirable locations. When this is added to the significant opportunity to develop new and exciting outcomes via AI, it is our opinion going to help the industry attract the staff it needs.
In the area of mining, do you observe a lively start-up scene?
The startup scene is very lively. It is a highly attractive area to work with, and given the embryonic state of AI in mining, the opportunities are vast. The challenge is to be relevant, having a great product is only the first step. A startup with a great idea can fail due to its size or exposure to the market. Mining wants the advantage of the innovation and agility of a startup, but risk mitigation is a clear challenge for the industry.
BASF is currently collaborating with the startup IntelliSense.io, a leading Industrial AI company, in order to optimize mining industry processes across the value chain. BASF brings to the partnership extensive mining knowledge, chemistry interaction expertise, and process excellence, whilst IntelliSense.io brings industry-leading advanced data analytics, software engineering, and mining industry experience that has been baked into our products. By combining the strengths of each origination, we can deliver all the benefits of both, and thus help to reduce the overall risk.
Thank you, Damien!
About Damien
Damien Caby is Senior Vice President at BASF, responsible for the global business unit Oilfield & Mining Solutions since 2017. Prior to joining BASF, Damien held several general management positions at Imerys, the world leader in industrial minerals. During his tenure at Imerys, he serviced a variety of specialty markets, including the polymer, food and beverage, oil & gas, pharmaceutical, automotive, construction, and refractory industries. Born in Paris, France, Damien received an engineering degree (applied mathematics) from Ecole Polytechnique and an engineering degree (business administration) from Ecole des Mines de Paris. He lives in Heidelberg, Germany, with his wife and 4 children.