Every single day wells are drilled whether for hydrocarbon, for water or for mining out of which resources are extracted. These drilling operations involve advanced technologies, different expertise, processes and people. With reserves being more complex and difficult to reach along with increasing difficult environment (Deep Off Shore, Sour environment, Extreme Weather conditions), wells not only cost more but also get people and equipment exposed to complex challenges.
While technologies evolved quickly towards safer, reliable and more accurate drilling equipment, real-time monitoring also contributed to better risk mitigation and performance improvement. Even though these changes helped improve drilling performances, they would need cutting edge technologies to go beyond and enable upcoming challenges about cost constraints, people management or risk mitigation.
Key challenges
With current turmoil, it is crucial for companies to drive cost down. For that matter, options are widely opened with essentially two ways to achieve that objective either thru enhanced performance and/or better supplier management. Performance improvement obviously begin with an optimal drilling plan that considers several parameters, may they be technical specifications, logistical constrains or regulatory and environmentally requirements. Although drilling plans are well prepared and designed at an early stage, it is however difficult to maintain up to date optimal plans with every day operation. For instance, a decision to sidetrack a well would have several impacts on all activities that could not be evaluated as detailed as the original drilling plan.
Additionally, performance improvement do not simply rely on faster drilling but rather drilling in an optimal way while mitigating risk. On that aspect, Big Data allow users to simulate scenarios for a better and more reliable decision process to save time, reduce cost and mitigate risk to people, equipment and environment.
Performance improvement do not rely on faster drilling but rather drilling in an optimal way #PredictiveAnalytics Click To TweetThere is no improvement if there is no Performance tracking - how else can we see the improvement? This second aspect is already largely deployed in the industry and there is no rig on earth that do not record time of operations daily. This common practice can further leverage the use of our digital age to help improving performance and to drive costs down. Often very little is done with the reports, this is specifically true with daily drilling reports that usually do not get analysed deep down to learn from past experiences.
In this blog post, we will therefore focus primarily on the two aspects of our digital drill and how analytics can improve drilling operations with Realtime Drilling Plans and how analytics based performance monitoring can help producing Stochastic Performance Benchmarking to drive cost down and improve performances.
The last approach toward drilling optimisation will be around predictive analytics and how we can use Advanced Predictive Analytics to predict events and again optimise performance on streaming data.
I love it when a plan comes together! (Hannibal – A-Team)
Unfortunately, things doesn’t always happen according to plans and when an event occurs, one need to react quickly under pressure and take optimal decisions to sort it out. Certainly, backup plans exist, but do they really cover all situations? These plans usually encompass reservoir and sub-surface disciplines, drilling engineering, equipment specifications and local regulations.
We can indeed recall the main traditional drilling design steps being:
Target Requirements with Well Objectives and Target definition
- Well Trajectory design during which one has to define the trajectory of the well with respect to technical constraints (dog leg severity, max deviation as well as safety concerns (distance btw wells for instance)
- Well Integrity design (casing and completion type, Mud rheology, cementation …)
- Well cost Evaluation from different scenario
- Well design selection that could be based on budget, time to completion or resources allocations
Planning a well is an iteration process that requires time and resources. DUe to different reasons (equipment shortage, new objectives, budget allocation modification) plans change and although that could be easy at the preparation stage, it would surely be more tedious and complex to perform while in operation.
Events during operation are numerous from stuck pipe requiring sidetrack to bad weather conditions that stop operations and force operators to change plans, to manage people and equipment as well as to change mobilisation of Service companies. In these conditions, one do not have the same amount of time nor resources to re-iterate the complete preparation cycle to take an optimal decision. Decisions such as mobilising new equipment or service companies, rerouting ship boats, freeing/allocating bed space or even defining alternate well design encompass several constraints from cost impact to logistic schedules.
Where humans consider few parameters, Big Data Analytics is able to use models and take into account a multi varied environment. It will strive to optimise recommendations that will empower decision makers to select scenarios that can encompass multiple constraints. Although frequently used within other industries, such optimisation solutions are usually “upgraded” with machine or deep learning algorithms that can fine tune the models along the way.
Operations would then benefit from an all-weather solution that enables recommendations based on current situation and bare able to notify people, service companies and resources, to update plan and evaluate cost/performance impact of each decision.
If you can't measure it, you can't improve it
Improving drilling performance starts with being able to consistently evaluate, track and monitor performances at the lowest granularity level possible and learn from it. For years, Daily Drilling Activity Reports have been produced from manual inputs recorded during operations. This has been used to document down and uptime and to derive Key Performance Indicators to compare performances between assets as well as to provide tangible targets to operations and service companies.
Indeed, this methodology present several challenges in terms of accuracy, repeatability and consistency because of:
- Manual recordings (DDR) which are not consistent nor accurate enough
- Lack of overall performance view from each well spread sheet
- Empiric Well Categories (like defining a complex well)
This information consolidated into one spreadsheet allow operators to filter performances by asset, localisation or service companies.
With vast range of possibilities, deep insights are often forgotten and minimum information extracted to only fill in monthly or quarterly reports.
Big Data Analytics propose wide opportunities to extract insights that would help operators to control their operations, challenge results with data driven information and improve performance and safety. A data driven approach proposes to apply analytics to:
- Automate identification of Activities (such as Drilling, Circulating, Reaming, Tripping, etc.) from data-driven rules (WOB, Bit movement, Torque, etc.)
- Monitor Drilling operations and derived KPI in real time
- Provide a systematic, consistent and agnostic approach across wells and service companies in multi environment
- Enable in situ/in context benchmark performances
- Simulate scenario to balance risk vs performance vs budget.
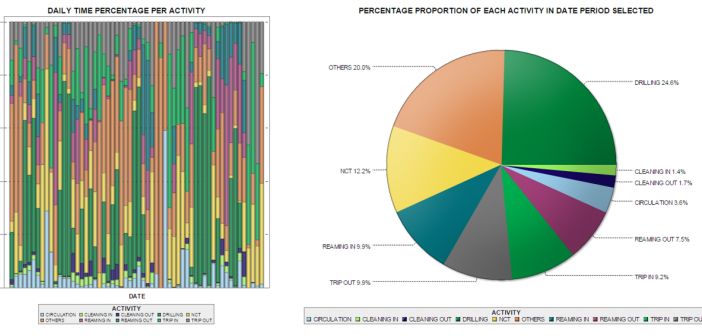
In fact, the process of detecting activities do no longer require one person on site to keep track of each activity time since that is automated from collection of rig streaming data to activity identification applying analytical rules. From there, standard industry KPIs are derived to offer users Real Time Performances Indicators.
Next step, historical data are analysed to define well complexity, key impacting parameters as well as building Performance Models. From those models, expected performances for each well/equipment specification can be defined. For instance, if we were to consider two wells both in the same formation in a 8 ½ in OH section with 40deg deviation drilled in OBM, the likelihood that performances would differ whether it is drilled offshore, at night with company A or B onto a fully automated rig or not is very high. In that case, big data analytics helps defining proper Benchmark Performances with regards to any drilling configuration (Well Requirements, Localization, Equipment and Third parties) using multi variate parameters. Big Data Analytics indeed allows a widening of matrix dimensions of parameters to analyse and to produce information at a lower granularity.
Thus, one operator could then accurately and consistently evaluate and predict performances to better manage and control its budget as well as optimising its operations with fact based NPT detection and ILT identification.
Beyond operational performance and real-time monitoring, this approach gets complete when applied to early planning phase during which what if scenario can be performed. For instance, getting that information beforehand would be very useful to simulate cost vs performance whether Company A or B is selected, so does it also apply similarly with Equipment usage.
2 Comments
David,
Have we met at SLB ? I had created NExT in the early 2000. Look forward discussing your SAS products. Thanks
Serge
Hi Serge,
I was at SLB between 2001 and 2012 mainly in North Africa and Continental Europe. I would be happy to discuss on how we can help.
Looking forward to continue this by email
Thanks
David