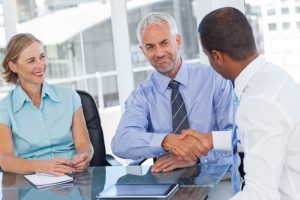
Manufacturing companies are undergoing a huge pressure to continually increase efficiency, productivity, lower costs, Net Working Capital and other KPIs. Strategies for doing so are many – lean strategies, improved forecasting and planning, closer supply chain collaboration to name a few. In this article, I will discuss the latter – and suggest that Analytics can play a key role in enhancing the benefit of supply chain collaboration.
Supply chain collaboration
Supply chain collaboration deals with how the interface between a customer and a supplier works. The most common areas to collaborate on are the ordering process, demand and production planning, (including VMI*), quality and in some cases product development.
If you try to investigate supply chain collaboration, you will soon run across different maturity models, typically suggesting 4-5 levels of integration. The relationship ranges from an “arms-length” relationship to a “fully integrated” or “optimized” scenario. The highest level of these maturity models has often been a visionary rather than a practically obtainable state.
Looking behind these maturity models, the relationship is defined by the level of
- data shared between the companies
- alignment of processes and decision making
The key to maturing the collaboration between two companies – thereby improving competitiveness of the supply chain is thus to increase these areas. Joint analytics falls naturally within these two categories, and will be able to enhance the benefit of the collaboration for the involved companies.
Analytics
On the SAS homepage, Analytics is defined as: “an encompassing and multidimensional field that uses mathematics, statistics, predictive modeling and machine-learning techniques to find meaningful patterns and knowledge in data.”
As stated in my earlier blogs around supply chain transparency I have advocated for the use of analytics to remove uncertainty. In these blogs I have covered e.g. visual analytics and predictive analytics as ways to support decision making. This can be within the areas of:
- Field quality – where quality reports are analyzed to find patterns in service reports. Case: Sub-zero
- Predictive maintenance – where data from manufacturing equipment is analyzed to identify patterns leading to need for maintenance – then applied in-stream. Case: Navistar or VR-Group
- Demand planning – where analytics are used to identify demand drivers and calculate forecasts. Case: Singapore National Library Board
- Inventory planning, where Analytics is used to optimize inventory levels to match supply chain uncertainties. Case: Nestle
There are naturally many other areas for using analytics in manufacturing companies.
While some manufacturing companies are just embarking the journey of analytics, and others are more experienced, the use of analytics as an area of improving supply chain collaboration is relatively un-documented.
Explore how artificial intelligence and machine learning applications are reshaping the supply chain of the future. Tune in to this on-demand webinar
Collaborative analytics example
Collaborative analytics can be seen as an extension of internal analytics – i.e. doing analytics with more data available and including data from a wider part of the value chain. This improves the ability to gain insights and thus build models that leads to cost saving, quality improvements or whatever is the subject of the analysis.
I will use Connected quality as an example
Connected quality is about removing scrap by analyzing and identifying the actual causes. Imagine a five-step production process. Imagine, that after step 4, materials are scrapped, due to product failure. By doing analytics, you can identify step 2 as the cause for failure – if certain events / readings appear. By monitoring and controlling step 2, it will be possible to improve yield.
Next, imagine that the step 2 process is located at your supplier. Doing analytics only on the internal production process will not lead to improvements in yield – but sharing data in the supply chain and doing collaborative analytics will.
How
It starts with trust… and it pretty much ends there as well.
In order for analytics to be a part of the supply chain collaboration, both companies have to make data available. Data may be related to the core business of each company, so it will require mutual trust to open up.
Secondly, reacting to the knowledge gained from the analytics in the companies will lead to changes – leading to a shift in the cost and benefit structure, which can challenge the collaboration. It then requires trust that profit and cost is shared in mutual benefit – and that the knowledge is applied to increase competitiveness.
In short: Create a place where data can be shared and analysed, form an analytics team (e.g. a virtual team) gain access to an analytics software package and start exploring into data.
Even if companies do not have any experiences with analytics, this can be a way to start. Building an analytical culture is not an easy task – however, doing so jointly with other companies can:
- Make it easier to get access to data scientist resources
- Develop the culture internally – as there is an external pressure as well to get going
- Help own IT to prioritise the data that truly adds value
We have seen collaborative analytics set up even across competitors – which is used for all-around optimisation. e.g. landbrugsinfo for agricultural datasharing and research (site in Danish) or within the hearing aid industry.
Joint analytics will be able to enhance the benefit of the collaboration for the involved companies. #ConnectedSupplyChain Click To Tweet* VMI: Vendor Managed Inventory, where inventory is physically located at the customer's site, but owned by the supplier. Ordering and payment = consumption.